Разработка технологии синтеза и исследование материалов для создания высокотемпературных топливных элементов с пленочным электролитом на основе диоксида циркония
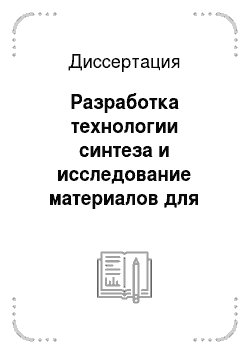
Диссертация
Из рассмотренных методик нанесения наиболее перспективными являются суспензионные методы. Был подобран оптимальный состав суспензии на клеевой основе из поливинилбутираля. Используемая суспензия обладает необходимыми качествами для наиболее эффективного нанесения благодаря, тщательному подбору состава. Достаточно высокая вязкость предотвращает затекание в поры подложки. Соответствующие… Читать ещё >
Содержание
- ГЛАВА I. ОБЗОР ЛИТЕРАТУРЫ
- 1. Краткое представление о высокотемпературных электрохимических устройствах на основе топливных элементов
- 2. Катод топливного элемента
- 3. Электролит топливного элемента
- 4. Методы формирования необходимых структур катода и электролита
- 5. Выводы из обзора литературы
- ГЛАВА II. РЕАГЕНТЫ И ИЗМЕРЕНИЯ
- 1. Реактивы, использованные в работе
- 2. Оборудование для высокотемпературной обработки
- 3. Оборудование для оценки свойств порошков и спеченных изделий
- ГЛАВА III. ЭКСПЕРИМЕНТАЛЬНАЯ ЧАСТЬ И ОБСУЖДЕНИЕ РЕЗУЛЬТАТОВ
- ЧАСТЬ I. МАНГАНИТ ЛАНТАНА-СТРОНЦИЯ
- 1. Получение манганита лантана-стронция
- 1. 1. Разработка технологии получения манганита лантана-стронция, основанной на методе осаждения из водных растворов
- 1. 2. Разработка технологии получения манганита лантана-стронция, основанной на методе термолиза нитратных солей
- 1. Получение манганита лантана-стронция
Список литературы
- Программа создания твердого оксидного топливного элемента фирмы Westinghouse, США. Отчет о результатах за 1989 год.
- Новиков Г. И., Гаманович H. М., Использование паров этилового спирта в качестве топлива в высокотемпературном топливном элементе. // Журнал прикладной химии. 1997, т.70, с. 1098−1101
- Гаманович H. М. Новиков Г. И. Электрохимическое окисление аммиака ввысокотемпературном топливном элементе. // Журнал прикладной химии. 1997, т.70, с. 1198−1199
- Пальгуев С. Ф., Гильдерман В. К., Земцов В. И. Высокотемпературные оксидные проводники для электрохимических устройств. Наука, 1990
- Thedmon С. S., Spacel H. S., Mitoff S. P., Cathode materials. // Journal of the Electrochemical Society. 1969, v. l 16, № 9, p. 1170−1175
- Doenitz W., Schmidberger R., Steinheil E. // Hydrogen energy system: Proc. II
- World hydrogen energy conference. Zurich. 1978, p.403−421
- Земцов В. И., Аникина Е. Л., Антонов Б. Д. Свойства сложных оксидов на основе хромитов неодима в окислительно-восстановительных средах. // Неорганические материалы. 1999, т.35, № 1, с.75
- Черепанов В. К., Бархатова Л. Ю., Кислородная нестехиометрия твердых растворов. // Неорганические материалы. 1998, т.34, № 11, с. 1314
- Тихонович В. Н., Хартон В. В., Наумович Е. Н. Особенности переноса кислорода в перовскитоподобных оксидах. // Неорганические материалы. 1997, т. ЗЗ, № 6, с.718
- Гайдук Ю. С., Хартон В. В., Наумович Е. Н., Самохвал В. В. Свойства твердых растворов Lao 6Sro, 4Mni.xNix03. // Неорганические материалы. 1994, т. ЗО, № 6, с.816−818
- Шаскольская М. П. Кристаллография. Москва. Высшая школа. 1976, с.167−292
- Raccah P. M., Goodenough J. В. // Phys. Rev. 1967, v.155, № 5, p.932−943
- Goodenough T. B. // Journal Appl. Physics. 1965, v36, № 3, pt 2, p.1031−1032
- Богданович H. M., Хомякова H. Г., Майзнер Е. А.,
- Третникова М. Г. Синтез и спекание манганитов лантана-стронция. // РАН УрО. Ионика твердого тела. 1993
- Полежаев Ю. М., Алямовская И. С., Марина Н. В. Технология твердых растворов. Свердловск. 1987
- Павлов В. И., Бычков Г. Л., Богуш А. К. Исследование кристаллической структуры манганитов Ьа.хМехМпОз.// Физические свойства газов и твердых тел. Минск. 1982, с.52−59
- Никитов В. А. Магнитные полупроводники и перспективы их использования в электронной технике. // Зарубежная электронная техника. 1977, № 12, с.3−35
- Yamamoto О., Takeda Y., Kanno R., Tamida Y. Electrode reaction of perovskite oxide Lai. xSrxMn03 for high temperature fuel cells. // Chemical Society of Japan. 1998, № 8, p. 1324−13 28
- Tagawa H. Mizusaki J., Katou M., et al. On the sold state reaction between stabilized zirconia and some perovskite oxides. // Proc. 2-nd International Symp. Solid Oxide Fuel Cells. Athens. 1991, p.681−688
- Yokogawa H., Sakai N., Kawada Т., Dokiya M. Thermodynamic analysis on interface between perovskite electrode and YSZ electrolyte. // Solid State Ionics. 1990, v.40/41, p.398−401
- Тихонова Л. А., Самаль Г. И., Жук П. П. и др. Физикохимические свойства манганита лантана, легированного стронцием. // Неорганические материалы. 1990, т.26, № 1, с. 184−188
- Jonker G. Н., Van Santen I. Н. Ferromagnetic compounds of Mn with perovskite structure. // Physika. 1950, v. 16, № 3, p.337−349
- Goodenough G. В., Wold A., ArnottR. J., Menyme N. Relationship between crystall symmetry and magnetic properties of ionic compounds containing Mn3+. Phys. Rev. 1961, v.24, № 2, p.373−384
- Wold A., Arnott R. J. Preparation and crystallographic properties of the systems ЬаМп1хМпхОз and LaMnNi03. // Journal of Phys. Chem. Solids. 1959, v.5, p.126−180
- Goodenough G. В., Loudo J. M. Crystallographic and magnetic properties of perovskite-related compounds. // Londolt Borustein, Fabellen, New Series III, Berlin. 1970, c.126−314
- Фесенко E. Г. Семейство перовскитов и сегнетоэлектричество. Москва. 4 Атомиздат. 1972
- Александров К. С. Последовательные структурные и фазовые переходы в перовскитах. 1. Симметрия искаженных фаз. Кристаллография. 1976, № 21, с.249−255
- Александров К. С., Позднякова JI. А., Орлова Т. А. Последовательные структурные фазовые переходы в перовскитах. 2. Искажение ячейки и смещение атомов. Кристаллография. 1977, № 22, с.93−100
- Goodenough G. В. Phys. Rev. 1933, v. 100, № 364
- Гегузин Е. Я. Физика спекания. Москва. Наука. 1967
- Третьяков Ю. Д. Твердофазные реакции. Москва. Химиздат. 1978
- Kertesz М., Reiss J., Tannauser D. S. et al. Structure and electrical conductivity of La0.84Sr0., 6MnO3. // Journal Solid State. 1982, v.42, p.125−129
- Minh N. Q. Ceramic fuel cells // Journal of the American Ceramic Society. 1993, v.76, № 3, p.563−568
- Севастьянов В. В. Исследование электрохимических ячеек с твердым оксидным электролитом, полученным по химической технологии. // ЗАО «Энергоцентр» г. Москва. 1997
- Панова Т. И., Малышева С. И., Дроздова И. А., Глушкова В. Б. Золь- гель синтез твердых растворов Zr02 с Y2O3. // Журнал прикладной химии. 1995, т.68, № 8, с.1385−1387
- Власов А. С. Разработка технологии порошков и керамических материалов с использованием новых методов. // Российский химический журнал. 1998, T. XLII, № 6, с. 152−156
- Kimiaki Tanihata, Yoshinari Miyamoto Synthesis ofPerovskite
- Type Lai. xSrxMn03 at low temperature. // Journal of the American Ceramic Society. 1992, v.75, № 1, p.201−202
- Tai-Lone Wen, Harlau A. U. Mixed cation oxide powders via resin intermediates derived from water-soluble polymer. // Journal of the American Ceramic Society. 1992, v.75, № 12, p.3490−3494
- Жигалкина И. А., Николаева Т. Д., Супоницкий Ю. Л., Поляк Б. И. Синтез хромита лантана золь-гель методом. // Стекло и керамика. 1998, № 6, с. 1517
- Полежаев Ю. М., Барбина Т. М., Полежаев В. Ю. Исследование совместно осажденных гидрооксидов циркония и элементов подгруппы скандия и лантаноидов при нагревании. // Неорганические материалы. 1994, т. ЗО, № 7, с.959−962.
- Комарь Н. П. Гетерогенные ионные равновесия. Харьков. 1984
- Лимарь Т. Ф. Химические методы синтеза и организация промышленного производства диэлектрических материалов. // Диссертация на соискание ученой степени доктора технических наук в форме научного доклада. Москва. 1985
- Тасаки Д. Одзаки Е. Мидзутани Н. Получение порошкообразных материалов из растворов. // Технология получения керамики. 1986, ч. Ш, с.2−3
- Цитович И. К. Курс аналитической химии. Москва. Высшая школа. 1994
- Алексеевский Е. В., Гольц Р. К., Мусакин А. П. Методы весового анализа. Госхимиздат. 1955, с.101−136
- Комарь Н. П. Основы качественного анализа катионов, т.1, 1955, с. 169 178
- Блок Н. И. Качественный химический анализ. Госхимиздат. с.59−71,114−117
- Надеинский Б. П. Теоретические обоснования и рассчеты в аналитической химии. Москва. 1956, с.220−265
- Бабко А. К. Растворимость осадков в присутствии общих и посторонних исков. // Журнал аналитической химии. 1952, т. VII, № 1, с.3−13
- Капустинский А. Ф. // Журнал прикладной химии. 1943, т.15, № 50
- Николаев А. В. Элентух М. П. Комплексное изучение осадков. // Журнал аналитической химии. 1952, t. VII, № 1, с.21−33
- Лурье Ю. Ю. Справочные таблицы для химиков
- Лурье Ю.Ю. Справочник по аналитической химии. Москва. 1971, с.94−104
- Химия и технология редких и рассеянных элементов. Часть II. Под ред. Большакова К. А. Москва. Высшая Школа. 1976
- Караваев Ю. Н., Неуймин А. Д., Панкратов А. А. Микроструктура твердых электролитов на основе частично стабилизированного и тетрагонального диоксида циркония // Неорганические материалы. 1999, том 35, № 12
- Kuwabara М., Ashizuka М., Kubota Y., Tsukidate Т. Degradation of the Electrical Properties of Y203-partially Stabilized Zirconia Ceramics
- Owing to Microcracking during Annealing // J. Mater. Sci. Lett. 1986, V.5, P. 7−9
- Hong-Yang La and San-Yuan Chem. Low-temperature Ageing of /-Zr02 Polycrystals with 3 mol. % Y203 // J. Am. Ceram. Soc. 1987, V.70, № 8, P. 537−541
- Lange P.P. Transformation-Toughened Zr02: Correlations between Cram Size Central and Composition in the System Zr02-Y203 // J. Am. Ceram. Soc. 1986, V.69, № 3, P. 240−242
- Саблина Т.Ю., Савченко H.A., Мельников А. Г., Кульков С. Н. Спекание в вакууме керамики на основе диоксида циркония // Стекло и керамика. 1994, № 5−6, С. 27−29
- Горелов В.П. Фазовая диаграмма системы Zr02-Y203 в области малых содержаний окиси иттрия // Тр. Ин-та электрохимии УНЦ АН СССР. 1978, Вып. 26, С. 69−75
- Jue J.F., Virkar A.V. Fabrication, Micro structural Characterization and Mechanical Properties of Poly crystalline t'-Zirconia// J. Am. Ceram. Soc. 1990, V.73, № 12, P. 3650−3657
- Badwall S.P.S. Zirconia-Based Solid Electrolytes: Microstructure, Stability and Ionic Conductivity // Solid State Ionics. 1992. V.52, P. 23−32
- Караваев Ю.Н., Неуймин А. Д. Твердые электролиты на основе частично стабилизированного диоксида циркония // Тез. докл. Всерос. конф. «Химия твердого тела и новые материалы» (14−18 октября 1996 г.). Екатеринбург. 1996, Т. 2, С. 190
- Караваев Ю.Н., Мартемъянова З. С., Зырянов В. Г. Влияние оксида железа на структуру твердых растворов системы Zr02 Y203 — Fe203 // Неорган, материалы. 1995, Т. 31, № 7, С. 937−941
- Караваев Ю.Н., Бурмакин Е. И. Влияние добавок оксида железа на электропроводность твердых электролитов на основе тетрагонального диоксида циркония в системе Zr02 Y2O3 // Неорган, материалы. 1996, Т. 32, № 1,С. 66−70
- Чеботин В.Н., Перфильев М. В. Электрохимия твердых электролитов. М., Химия, 1978. 312 с.
- Рутман Д. С., Торопов Ю. С., Плинер С. Ю. и др. Высокоогнеупорные материалы из диоксида циркония . М., Металлургия. 1985, 136 с.
- Бакунов В. С., Балкевич В. Д., Власов А. С. и др. Керамика из
- Дубок В. А, Кабанова М. И., Недилько С. А., Панченко Г. В. Влияние метода синтеза на свойство порошков частично стабилизированного диоксида циркония // Порошковая металлургия. 1988, № 8 высокоогнеупорных окислов. М., Металлургия. 1977, 304 с.
- Арсеньев П. А., Глушкова В. Б., Евдокимов А. А. и др. Соединенияредкоземельных элементов. Цирконаты, гафнаты, ниобаты, танталаты, антимонаты. М., Наука. 1985, 261 с.
- Garvie R. С., Nicholson P. S. Phase analysis in zirconia systems //J. Amer. Ceram. Soc. 1972, 55, N 6, P. 303—305
- Палатник А. С. Структура и физические свойства твердого тела. Лабораторный практикум. Киев, Вища школа. 1983, 264 с.
- Пинес Б. Я. Лекции по структурному анализу. Харьков, Изд-во Харьк. ун-та. 1967, 478 с.
- Кравчик Е, А., Мошкина Т. И., Осмаков А. С. Определение параметров тонкой структуры в порошках и опилках вольфрама методом гармонического анализа рентгеновских дифракционных линий // Завод, лаб. 1986, № 6, С. 43—47.
- Миркин Л. И. Справочник по рентгеноструктурному анализу поликристаллов. М., Физматгиз. 1961, 863 с.
- Вишняков Я. Д. Современные методы исследования структуры деформированных кристаллов. М., Металлургия. 1975, 470 с.
- Takao I. Particle and crystallite sizes of Zr02 powder obtained by the calcination of hydrous zirconia//J. Mat. Sci. Lett. 1985, N 4, P. 431—433
- Roosen A., Hausner H. Sintez von zirkondioxid bei niedrigen temperaturen // CFI/Ber. DKG. 1985, 62, N 4/5, P. 184—192
- Lange F. F. Transformation toughening. 3. Experimental observations in the Zr02 — Ya03 system // J. Mat. Sci. 1982, N.17, P. 240—246
- Васильев Д. M. Дифракционные методы исследования структур. М., Металлургия. 1977, 247 с.
- Gilti G., Borea P. A. Effect of non-linearity error in the warren-averbach analysis // J. Appl. Cryst. 1973, N.6, P. 203—206
- Пинес Б. Я., Суровцев И. Я. К вопросу об определении дисперсности и микроискажений кристаллической решетки по данным гармонического анализа формы линий рентгенограмм // Кристаллография. 1963, 8, № 3, С. 489—493
- Соловким А. С., Ягодин Г. А. Итоги науки. Неорганическая химия. Том 1. М., ВИНИТИ. 1969
- Соловкин А. С., Ягодин Г. А. Итоги науки. Неорганическая химия. Том 2. М., ВИНИТИ. 1970
- Головкин А. С., Цветкова 3. Н. // Успехи химии. 1962, 31, 1394
- Larsen Е. М. // Adv. Inorg. Chem. and Radiochem. Vol. 13, New-York-London, 1970, p. 1
- MacDermott T. S. // Coord. Chem. Revs. 1973, 11,1
- Kepert D. L. // Proc. Roy. Aust. Chem Inst. 1970, 135
- Barraclouch C. G., Lewis J., Nyholm R. S. // J. Chem. Soc. (London). 1959, 3552.
- Мак Т. C. W. // Canad. J. Chem. 1968, 46, 3491
- Савенко H. Ф., Шека И. А., Матяш И. В., Калининенко А. М, // Укр. хим. ж, 1972,38, 146
- Спасибенко Т. П., Горощенко Я. Г. //Ж. неорган, хим. 1969, 14, 1447
- Лебедева Е. Н., Коровин С. С., Томилов Н. П., Петров К. И. // Ж. неорган, хим. 1971, 16, 666
- Прозоровская 3. Н., Потапова И. В., Калинина С. С., Чуваев В. Ф., Петров К. И., Комиссарова Л. Н. // Ж. неорган, хим. 1972, 17, 2940
- Прозоровская 3. Н., Комиссарова Л. Н., Шестакова Т. В. // Ж. неорган, хим. 1970, 15,335
- Карлышева К. Ф., Кошель А. В., Шека И. А., Семенова Г. С. // Ж.неорган, хим. 1975, 20, 932
- Siedle A. R. // J. Inorg. Nucl Chem. 1973, 35, 3429
- Панкратова Л. Н., Харитонова Г. С. Н Ж. неорган, хим. 1972, 17, 3227
- Florence Т. М., Farrar Y. J., Zittel Н. Е. // Austral. J. Chem. 1969, 22, 2321.
- Карлышева К. Ф., Кошель А. В., Малинко Л. А., Шека И. А. // Ж. неорган, хим. 1970, 15, 1825
- Pande С. S., Misra G. N. // Indian J. Chem. 1973, 11, 292
- Каминский Б. Т., Плыгумов А. С., Прокофьева Г. Н. // Укр. хим. ж. 1973,39, 946
- Чекмарев А. М., Чибрикин В. В., Ягодин Г. А. /У Радиохимия. 1975, 17, 165.
- Noren В. // Acta chem. Scand. 1973, 27, 1369
- Duda J., Maslowska J. // Rozn. Chem. 1973, 47, 1337.
- Чухланцев В. Г., Полежаев Ю. M.//Ж. прикладн. хим. 1969
- Fryer J. R., Hutchison J. L., Paterson R. // J. Colloid. Interface Sci. 1970, 34, 238
- Bettinali C., Ferrafesso G. // J. Amer. Ceram. Soc. 1970, 53, 495
- Рейнтен X. Г. В сб.: «Строение и свойства адсорбентов и катализаторов». М., Мир. 1973, с.332
- Закирова А. В., Коленкова М. А., Сажина В. А., Стрижко А. С. // Изв. высш. учеб. завед. Цвет. мет. 1969, № 5,77
- Чухланцев В. Г., Галкин Ю. М. // Ж. неорган, хим. 1073, 18, 1456
- Годнева М.М., Мотов Д. Л. // Ж. неорган, хим. 1971, 16, (40, 41)
- Годнева MJVL, Мотов Д. Л. Охрименко Р.Ф. // Ж. неорган, хим. 1973, 16
- Савенко Н. Ф., Шека И. А., Матяш И. В., Калининенко А. М, // Укр. хим. ж. 1973, 39, 79
- Зайцев Н.М. // Ж. неорган, хим. 1966, 11, 1684
- Blumenthal W. В. // J. Less-Common. Metals. 1973, 30, 39
- Minh N.Q., pp. 652 63, in Science and Technology of Zirconia V, Ed. by S.P.S. Badwal, M.J. Bannister, R.H.J. Hannink, Technomic Publishing, Pennsylvania, 1993
- Minh N.Q., Armstrong T.R., Esopa J.R., Guiheen J.V., Home C.R. andvan Ackeren J.J., pp. 801−8, in Proc. 3rd. Intl. Symp. Solid Oxide Fuel Cells, Ed. by S.C. Singhal and H. Iwahara, The Electrochem. Soc., Proc. Vol. 93−4, 1993
- Milliken C., Elangovan S., and Khandkar A.C., pp. 466 477, in Proc. 2nd. Intl. Symp. Ionic and Mixed Conducting Ceramics, Ed. by T.A. Ramanarayanan, W.L. Worrell, and H.L. Tuller, The Electrochem. Soc.1. Proc. Vol. 94−12, 1994
- Godickemeier M., Sasaki K., Bohac P., and Gauckler L.J., pp. 225 34, in Proc. 6th 1EA-Workshop Advanced SOFCs, Rome Italy, 1994
- Bossel U.G. Facts & Figures. Swiss Federal Office of Energy. Bern Switzerland, 1992
- Sasaki K., Phase Equilibria, Electrical Conductivity, and Electrochemical Properties of Zr02 ln203, Ph.D. Thesis, Swiss Federal Institute of Technology Zurich, 1993
- Ackerman J.P. and Young J.E., U.S. patent, No. 4 476 198, Oct. 9, 1984.
- Otsuka K., Multilayer Ceramic Substrate-Technology for VLSI Package. Multilayer Module, Elservier, 1991.
- Young W.S. and Knickerbocker S.H., pp. 489−526, in Ceramic Materials for Electronics, Ed. by. Buchanan R. C, Marcel Dekker, New York, 1991
- Pal U.B. and Singhal S.C. // J. Electrochem. Soc., 137, 2937 41, 1990
- Thiele E.S., Wang L.S., Wang Т.О., and Barnett S.A. //J. Vac. Sci. Technol., 49 3054−60, 1991
- Smidt F.A., Intl. Mater. Rev., 35 61−129 (1990).
- Kokai F., Amano K., Ota H., Umemura F. // Appl. Phys., A54 340−42 1992
- V.E.J, van Dieten, Walterbos P.H.M. and Schoonman J., pp. 183 91, in Proc. 2nd Intl. Symp. Solid Oxide Fuel Cells, Ed. by F. Grosz, P. Zegers, S.C. Singhal and O. Yamamoto, Commission of European Communities, 1991
- Nakagawa K., Yoshioka H., Kuroda C., and IshidaM., // Solid State Ionics, 35, 249−55, 1989
- Sturgeon A J. Materials World, 1 (6) 351−54 1993.
- Sasaki K., Bohac P. and Gauckler L.J., Extended Abstract, 2nd Expert Meeting of IEA-SOFC Task, Swiss Federal Office of Energy, Bern, Switzerland, 1990
- Rothman E.P. and Bowen H.K. pp. 17−34, in Mater. Res. Soc. Symp.Proc. Vol. 60, 1986.
- Mori M., Itoh H., Mori N., Abe Т., pp. 61−64, in Proc. 1st. Symp. SOFC Тяпяп 199?.--Г---—з — -
- Graule Th., Baader F., and Gauckler L.J., Ceramic Forum International, Deutsche Keramische Gesellschaft, 71 (6) 317−23, 1994
- Фридрихсберг Д.А. Курс коллоидной химии. Ленинград, Химия, 1984, 368 с.
- Фролов Ю.Г. Курс коллоидной химии. Поверхностные явления и дисперсные системы. М., Химия, 1984, 368 с.
- Техническое задание на разработку и поставку исходных материалов и элементов технологии для изготовления твердооксидных топливных элементов. ГНЦ РФ ФЭИ им. акад. А. И. Лейпунского, г. Обнинск, приложение к договору о сотрудничестве, 1998−2001г.г.
- Шаталов В. В. Скороваров А.С. Экологически безопасная технология получения манганита лантана-стронция для катода высокотемпературного топливного элемента. II Известия академии промышленной экологии, 2001, № 2, с. 53.137
- Скороваров A.C. Технология получения манганита лантана-стронция. // Тезисы докладов. Конференция молодых ученых и специалистов, посвященная 50-летию ВНИИХТ, 6.03.2001, ЦНИИатоминформ, с. 26.
- Либенсон Г. А. Основы порошковой металлургии. М., Металлургия, 1987, 256с.
- Григорьев А. К. Рудской А.И. Деформация и уплотнение порошковых материалов. М., Прогресс, 1992, 248с.
- Джонс В.Д. Основы порошковой металлургии. Прессование и спекание. Пер. с англ. М., Металлургия, 1965, 324 с.
- Скороваров A.C. Пористые подложки из манганита лантана-стронция // Химическая технология, 2002, № 4, с. 2148.
- Балкевич B.JI. Техническая керамика. М., Изд-во лит-ры по стр-ву, 1968, 200 с.
- Безбородое М.А., Ермоленко H.H. Циркониево-бариевые стекла. Минск. 1959,32 с.
- Урьев Н.Б., Потанин A.A. Текучесть порошков и суспензий. М., Химия, 1992,256 с.
- Борисенко А.И., Николаева JI.В. Тонкослойные стеклоэмалевые и стеклокерамические покрытия. Ленинград, Наука, 1970, 70 с.