Совершенствование технологии изготовления коленчатых валов форсированных дизелей на основе применения дифференцированного гидродробеструйного упрочнения и композиционных материалов
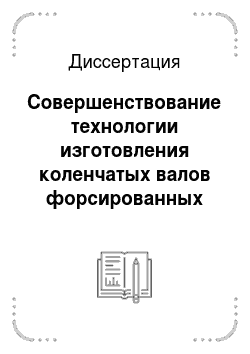
Результаты исследований напряженного состояния элементов коленчатых валов в условиях знакопеременного циклического нагружения с применением МКЭ позволяет более верно судить об эксплуатационной надежности конструкции по критерию «усталостная прочность». Показано, что технологические процессы механической обработки, дифференцированного гидродробеструйного упрочнения наряду с микрогеометриеп… Читать ещё >
Содержание
- 1. СОСТОЯНИЕ ВОПРОСА И ЗАДАЧИ 15 ИССЛЕДОВАНИЯ
- 1. 1. Оценка основных опубликованных материалов по 15 методам н моделям повышения эксплуатационной надежности элементов коленчатого вала
- 1. 2. Объекты исследований
- 1. 3. Прогнозирование живучести коленчатых валов ДВС
- 1. 3. 1. Прогнозирование жизненного цикла коленчатых валов по 27 критерию «вероятность безотказной работы»
- 1. 3. 2. Оценка жизненного цикла коленчатых валов по 30 критерию механики разрушения
- 1. 4. Цель работы и задачи исследования
- 2. ТЕОРЕТИЧЕСКИЕ ТЕХНОЛОГИЧЕСКИЕ 33 ХАРАКТЕРИСТИКИ ПРИ ОЦЕНКЕ КРИТЕРИЕВ ПОВЕРХНОСТНОГО ПЛАСТИЧЕСКОГО ДЕФОРМИРОВАНИЯ ЭЛЕМЕНТОВ КОЛЕНЧАТЫХ ВАЛОВ
- 2. 1. Расчетные методы оценки основных технологических 33 критериев поверхностного пластического деформирования образцов-свидетелей
2.2 Теоретическая оценка начальных технологических 40, остаточных напряжений в поверхностном слое элементов коленчатого вала двигателя внутреннего сгорания после технологического дифференцированного поверхностного пластического деформирования
2.3 Теоретическая оценка формирования начальных 47 технологических остаточных напряжений при ППД с применением метода конечных элементов
3 РАЗРАБОТКА МЕТОДИЧЕСКИХ УКАЗАНИЙ И 64 ЭКСПЕРИМЕНТАЛЬНАЯ ПРОВЕРКА НАПРЯЖЕННОГО СОСТОЯНИЯ ЭЛЕМЕНТОВ КОЛЕНЧАТОГО ВАЛА
3.1 Усталостная прочность коленчатых валов 64 форсированных дизелей
3.2 Исследование параметров дефектного слоя в материале 70 элементов коленчатого вала в условиях эксплуатации, оборудование и приборы
3.2.1 Технологический метод определения остаточных 70 напряжений в поверхностном слое детали
3.2.2 Влияние комбинированного поверхностного 77 упрочнения на начальные технологические остаточные напряжения в стали
3.3 Напряженное состояние элементов коленчатого вала в 85 условиях эксплуатации, оборудование и приборы
3.3.1 Режимы поляризации и технология изготовления 85 моделей коленчатых валов
3.3.2 Моделирование напряженного состояния и 89 теоретических коэффициентов концентрации напряжений коленчатого вала форсированного дизеля
4 НАГРУЖЕННОСТЬ ЭЛЕМЕНТОВ КОЛЕНЧАТЫХ 93 ВАЛОВ
4.1 Условия работы коленчатых валов
4.2 Распределение напряжений в противовесах и щеках 95 коленчатых валов
4.3 Торсиографирование крутильных колебаний коленчатых 102 валов форсированных дизелей
5 РАЗРАБОТКА И ОБОСНОВАНИЕ ТЕХНОЛОГИЧЕСКИХ МЕТОДОВ И СРЕДСТВ ПОВЫШЕНИЯ ЭКСПЛУАТАЦИОННОЙ НАДЕЖНОСТИ ЭЛЕМЕНТОВ КОЛЕНЧАТОГО ВАЛА
5.1 Повышение усталостной прочности коленчатых валов 110 форсированных дизелей малоотходными технологическими методами
5.2 Дифференцированная гидродробеструйная обработка 120 элементов коленчатого вал а
5.2.1 Дифференцированное гидродробеструйное упрочнение 120 наружных поверхностей щеки и противовеса коленчатого вала форсированного дизеля
5.3 Методика планирования экспериментов и обработка 128 экспериментальных данных при дифференцированной гидродробеструйной обработке элементов коленчатых валов форсированных дизелей
5.4 Технико-экономическое обоснование технологических 135 методов повышения эксплуатационной надежности противовесов и щек коленчатых валов форсированных дизелей
5.4.1 Годовой экономический эффект от внедрения 135 дифференцированного гидродробеструйного упрочнения противовесов и щек коленчатых валов форсированных дизелей
5.4.2 Годовой экономический эффект от внедрения 140 термопластичного композиционного материала в технологию демпферов крутильных колебаний коленчатых валов форсированных дизелей
ОСНОВНЫЕ ВЫВ ОДЫ
Список литературы
- A.c. № 179 062. Многоместная инерционная установка для испытаний подшипников /А.Б. Курицын // Бюллетень изобретений, открытий и товарных знаков, № 19.1977.-е. 150-
- A.c. № 1 236 216. Тонкостенный бесканавочный вкладыш /Косырев С.П., Гребнев В.М.//Бюллетень изобретений, открытий и товарных знаков, № 21.1986.-c.75-
- A.c. № 1 446 375. Вкладыш подшипника скольжения высокофорсированного дизеля /Косырев С.П., Ким Ф.Г.//Бюллетень изобретений, открытий и товарных знаков, № 47.1988.-с.73-
- A.c. № 1 530 847. Тонкостенный вкладыш подшипника скольжения высокофорсированного дизеля /Косырев С.П., Кочерженко В. Г., Гребнев В.М.//Бюллетень изобретений, открытий и товарных знаков, № 41.1989.-c.132-
- A.c. № 1 657 785. Биметаллический материал для подшипников скольжения /Косырев С.П., Ким Ф. Г., Гребнев В. М., Козлов В.Ф.//Бюллетень изобретений, открытий и товарных знаков, № 23.1991.-c.49-
- Буше H.A., Подшипниковые сплавы для подвижного состава. М.: Транспорт, 1967. — 224 с.
- Буше H.A., Мудренко Г. А., Двоекина В. А., Повышение долговечности изделий из сплавов цветных металлов // Труды ВНИИЖТ, 1972, вып.473 с. 74−77-
- Буше H.A., Копытько В. В., Совместимость трущихся поверхностей. -М.: Наука, 1981.- 126 е.-
- Буше H.A., Гуляев A.C., Двоекина В. А., Подшипники из алюминиевых сплавов. -М.: Транспорт, 1984. с.75−80-
- Буше H.A., Трение, износ и усталость в машинах. Транспортная техника. М.: Транспорт, 1987. — 223 е.-
- Биргер И.А., Расчет на прочность детален машин: Справочное пособие// И. А. Биргер, Б. Ф. Шорр, P.M. Шнейдерович. М.: Машиностроение, 1969. -459с.-
- Ваншейдт В.А., Иваноченко H.H., Колеров В. К., Справочник «Дизели».- М.: Машиностроение, 1999. 599 е.-
- Воронов В.Д., Подшипники сухого трения. JL: Машиностроение, 1979.-78 е.-
- Влияние диссипативных и объемных свойств смазочных материалов на эффективность их применения / Д. Г. Громаковский // Химия и технология топлив и масел. 1985, № 11.-е. 37−39-
- Василевский Б.И., Дискретная модель и граничные условия в расчете шатуна методом конечных элементов / Б. И. Василевский, тр. ЦНИДИ. -Л.: 1997, № 259-
- Григорьев М.А., Долецкий В. А., Обеспечение надежности двигателей.- М.6 Издательство стандартов, 1978. с.301-
- Гурвич И.Б., Сыркин П. Э., Эксплуатационная надежность автомобильных двигателей. М.: Транспорт, 1984. — 141с.-
- Деркаченко В.Г., Загружной А. П. и др., Исследование усталостной прочности подшипниковых материалов на стенде СПП — 1 конструкции ЦНИДИ. Тр. ЦНИДИ, вып. 65, 1972. с. 41−49-
- Дьяков А.К., Подшипники скольжения жидкостного трения. М. Машгиз, 1955. — 320 е.-
- Денисов A.C., Кулаков А. Т., Анализ причин эксплуатационных разрушений шатунных вкладышей двигателя КамАЗ 740 // Двигателестроение. 1981, № 9. — с. 37−40-
- Захаров С.М., Никитин А. П., Загорянский Ю. А., Подшипники коленчатых валов тепловозных двигателей. М.: Транспорт, 1981.179 е.-
- Захаров С.М., Эрдман В. Ф., Гидродинамический и тепловой расчет подшипников коленчатого вала поршневого двигателя // Вестник машиностроения, 1978, № 5. с. 24−28-
- Зайцев А.К., Основы учения о трении, износе и смазке машин. М. -Л.: Машгиз, 1947. — 256 е.-
- Зундема Г. Г., Эксплуатационные свойства смазочных масел. — М.: Гостехиздат, 1957. с. 21−27-
- Изотов А.Д., Применение прямых вариационных методов к расчету нестационарно нагруженных цилиндрических подшипников. — Тр. ЦНИДИ, 1978, вып. 73. — с. 5−13-
- Исследование работы подшипников скольжения на основе анализа траектории центра вала/ Экспресс информация «Детали машин». -М.: 1984, № 5.-с. 6−18-
- Карасик П.П., Прирабатываемость материалов для подшипников скольжения. М.: Наука, 1975. — с. 135-
- Клокова Н.П., Тензодатчики для измерения при повышенных температурах. — М.: Машиностроение, 1965. — 120 е.-
- Косырев С.П., Концентрация напряжений в кривошипной головке шатуна высокофорсированного дизеля и способы ее нейтрализации // Изв. ВУЗов. Машиностроение. 1988, № 11. с. 77−81-
- Косырев С.П. Динамическое нагружение кривошипно-шатунного механизма дизелей // Двигателестроение. 1980, № 11.-е. 21−23-
- Косырев С.П., Сорокина JI.A., Рафиков P.M., Комиссаренко Е.А.,
- Технологические проблемы обеспечения работоспособностинагруженных деталей высокофорсированных дизелей // Современные148проблемы технического сервиса в агропромышленном комплексе: Междунар. научно-практ. конф. М.: МГАУ, 2003. — с. 17−19-
- Кузнецов Е.С. Управление технической эксплуатацией автомобилей. — М.: Транспорт, 1990.-272 е.-
- Кудрявцев И.В., Основы выбора режима упрочняющего поверхностного наклепа ударным способом // Тр. ЦНИИТМАШ, 1965, кн. 108.-е. 57−62-
- Коднир Д.С., Контактная гидродинамика смазки деталей машин. М.: Машиностроение, 1976. — с. 26−30-
- Коровчинский М.В., Теоретические основы работы подшипников скольжения. М.: Машгиз, 1959. — 404 е.-
- Крагельский И.В., Трение и износ. М.: Машиностроение, 1968.-480 е.-
- Костецкий Б.И., Трение, смазка и износ в машинах. Киев: Техника, 1970.-385 е.-
- Каратышкин С.Г., Динамически нагруженные подшипники судовых двигателей внутреннего сгорания. М.: Судостроение, 1968. — 182 е.-
- Косьтрев С.П., Горшков Е. А. Моделирование напряженного состояния поршневой головки шатуна форсированного дизеля// Двпгателестроение.- 2007, — № 3.- С. 14−15.
- Косырев С.П., Марьина H.JL Повышение эксплуатационной надежности коленчатых валов высокофорсированных дизелей технологическим методом// Проблемы прочности, надежности, эффективности/ Сборник научных трудов.: Саратов: 2007 с 24−26
- Косырев С.П., Марьина Н. Л. Усталостная прочность коленчатых валов форсированных дизелей// Сборник трудов 9 Российской научнойконференции: Векторная энергетика в технических, биологических и социальных системах.: Саратов: 2007 с 11−13-
- Косырев С.П., Кудашева И. О., Марьина Н. Л. Моделирование напряженного состояния коленчатого вала форсированного двигателя// Двигателестроение.: Санкт Петербург: 2008, с 9−11-
- Косырев С.П., Кудашева И. О., Марьина Н. Л. Технологический метод определения остаточных напряжений в поверхностном слое детали// Материалы XII Международной научно-практической конференции: Современные технологии в машиностроении.: Пенза: 2008, с 34−36-
- Косырев С.П., Кудашева И. О., Марьина Н. Л. Повышение усталостной прочности коленчатых валов форсированных дизелей малоотходными технологическими методами//Ремонт, восстановление, модернизация: Москва: 2009, № 9-
- Косырев С.П., Кудашева И. О., Марьина Н. Л. Влияние комбинированного поверхностного упрочнения на начальные технологические остаточные напряжения в стали// Вестник саратовского государственного технического университета: Саратов: 2009, № 2-
- Косырев С.П., Кудашева И. О., Марьина Н. Л. Торсиографирование крутильных колебаний коленчатых валов двигателей и агрегатов на их базе// Материалы семинара/ Материалы межгосударственного научно-технического семинара. Выпуск 22.: -Саратов: СГАУ: 2009-
- Курицына А.Д., Истомин И. П., Композиционные материалы и покрытия на базе фторопласта — 4 для сухого трения в подшипникахскольжения. М.: машиностроение, 1974. — с. 57- 61−151
- Лукинский B.C.. Разработка методов обеспечения надежности большегрузных автомобилей на стадии проектирования: Диссертация доктора технических наук. Л.: ЛСХИ, 1985. — 413 е.-
- A.W.J. Materials research and tribology. TNO, 1971, № 8. p. 445 — 445.-
- Михайлов A.M., Сопротивление материалов. M.: Стройиздат, 1989. -с. 85-
- Мошков А.Д., Пористые антифрикционные материалы. М.: Машиностроение, 1968. — с. 34−42-
- Медвинский М.Д., Трехканальный усилитель типа ПТМП 3 — 55 для измерения толщины масляной пленки в подшипниках жидкостного трения. — Тр. ЦНИИТМАШ, 1958, № 9. — с. 18−21-
- Орлин A.C., Расчет напряженно-деформированного состояния поршней / A.C. Орлин, H.A. Иващенко, A.B. Тимохин // Известия ВУЗов. Машиностроение, 1977, № 5. с. 73−78-
- Одинцов Л.Г., Упрочнение и отливка деталей поверхностным пластическим деформированием: Справочник. М.: Машиностроение. 1987.-327 е.-
- Овсеенко А.Н., Серебряков В. И., Гаек М. М., Технологическое обеспечение качества изделий машиностроения. — М.: УМО AM, 2004. 296 е.-
- Овсеенко А.Н., Кпюшин А. Р., Состояние поверхностного слоя лопаточных материалов после различных видов деформированного упрочнения // Тр. ЦНИИТМАШ, 1989, кн. 105. с. 73−79-
- Прокопьев В.Н., К расчету опорных подшипников, нагруженных силами, переменными по величине и направлению. Машиностроение, 1978, № 5.-с. 105−108-
- Партон В.З., Морозов Е. М., Механика упруго-пластического разрушения. — М.: Наука, 1974. 246 е.-
- Петросов В.В., Упрочнение лопаток газотурбинного двигателяобработкой дробью. // Влияние технологических факторов на качество152и надежность лопаток турбин: Материалы совещания. М.: 1962. — с. 138- 154-
- Патент РФ № 2 133 282. Способ стабилизации напряжений в поверхностном слое детали / Косырев С. П. и др. // Бюллетень изобретений, открытий и товарных знаков, № 20. 1999 27 с-
- Патент РФ № 2 304 244. Термопластичный демпфер крутильных колебаний двигателя внутреннего сгорания/ Марьина H.JI./ Росскомитет. Москва. 2007-
- Российский Морской Регистр Судоходства. Правила классификации и постройки морских судов. Т.2,2003.
- Рудницкий Н.М., Рассадин Ю.А" Курицына А. Д., Изготовление и испытание подшипников с антифрикционным слоем из высокооловянистых алюминиевых сплавов // Тр. НАМИ, 1966, вып. 82. с. 50−70-
- Ротенберг Р.В. Основы надежности системы водитель автомобиль — дорога — среда. — М.: машиностроение, 1987. 216 с.-
- Рекомендации по применению процесса поверхностного упрочнения деталей машин. М.: Тр. ЦНИИТМАШ, 1981.-14 е.-
- Снеговский Ф.П., Расчет и конструирование подшипников скольжения. -Киев: Техника, 1974. 123 е.-
- Суркин В.И., Попов Т. П., Оптимизация параметров шатунного подшипника тракторного дизеля // Двигателестроение. 1984, № 3. с. 41−43-
- Семенов А.П., Савинский Ю. Э., Маталлофторштастовые подшипники.-М.: Машиностроение, 1976. 123 е.-153
- Смелянский В.М., Механика упрочнения деталей поверхностным пластическим деформированием. М.: Машиностроение, 2002. — 299 е.-
- Тузов Л.В., Скориков Ю. Т. Чирков И.М., Расчетное определение упругих характеристик подшипников скольжения// Двигателестроение, 1987, № 9.-с. 18−19-
- Тимошенко С.П., Дж.Гере. Механика материалов. 0 М.: Мир, 1976.-С.222−223.
- Файнгольд Н.Ш., Аксельрод М. Л., Виноградова И. К., Малогабаритный датчик для измерения давления и температуры масляного слоя подшипников скольжения. М.: НИИИНФОРМТЯЖМАШ: 1971, № 12.-е. 12−14-
- Рубин М.Б., Бахарева В. Е., Подшипники в судовой технике. Л.: Судостроение, 1987.-е. 16−17-
- Хрущев М.М., Классификация условий и видов изнашивания деталей машин// Трение и износ в машинах. М.: Изд-во АН ССР, 1953, вып. 3. -с. 5−17-
- Хрущев М.М., Бабичев М. А., Абразивное изнашивание. М.: Наука, 1970.-252 е.-
- Чистяков В.К., Динамика поршневых и комбинированных двигателей внутреннего сгорания. М.: Машиностроение, 1989. — с. 215 — 216-
- Чернавский С.А., Подшипники скольжения. М.: Машгиз, 1963. — 238 е.-
- Ценев В.А., голованов О.И., Тензодатчики с температурной компенсацией для высокотемпературного тезометрирования деталей двигателей// Исследование работы энергетического оборудования. -Калинин: 1973. с. 71−78-
- Яковлев В.Ф., измерение деформаций и напряжений в деталях машин. -М.- Л.: 1963.- 144 е.-
- Эффективные методы снижения трения // Машины и механизмы: Обзорная информация / Черметинформация, 1976. 57 е.-
- Юргенсон A.A., Зелинская Г. И., Металлы быстроходных дизелей и их термическая обработка. М.: Машиностроение, 1967. — 120 е.-
- Дж. Мейз. Теория и задачи механики сплошных сред. М.: Мир, 1974.- с. 248−257-
- Metals Handbook, W, Propenties and Selection of Metals. -1961/ h. 843−851-
- Hodes E. Outbon von tiblechen Frockenlageru ans Mettals Kunststoff ver bunndwerkstoffen, 1973, № 79-
- Block H. Les temperatures de surface dan des conditions de graissage sous extreme pression. Congr. mon did du petrol. Paris. Ill, 1937, h. 13−23-
- Desvaux M. P. E. Development of a high-tin aluminium plain bearing material. Reprinted from Fribology, April, 1972, p. 61−66-
- Dinger H. Das hydridynamosche Verhalten der Pleuellager. Diss. Stuttgart. Tech. univ., 1955-
- Grobuschek F., Ederer U. Optimited Engine Bearing Design by Evaluating Performance. Diesel and Cas Turbine Progress Worldwide, October, 1978, p. 19−20-
- Hahn H.W. New Calculation Methods for Engine Bearings. SAE, Automative Engineering Congress, Paper 660 033, 1966, p. 1−21-